Form follows function in materials design

How do you find the right material to build the best product? ASU engineers are turning the typical trial-and-error process on its head.
Suppose you want to build something — a skyscraper or a spacecraft, a computer or a car, a water bottle or a wristwatch.
You’ll need materials to make that product, and you’ll need to choose the best materials for the job. For instance, you’ll want lightweight materials for a spacecraft so that you can afford to propel it out of Earth’s gravity. But if it will come back to Earth, it also needs to withstand the heat of re-entry.
How do you find the right material to suit your needs? Generally, it takes a lot of trial and error. You make a material and you test it in a lab. Crush it. Cook it. Stretch it. Chill it. Then do it over and over and over again.
It is a time-consuming and expensive process. And although you’ll probably find a material that suits your purpose, it might not be the best possible material for the job.
That’s why a group of researchers at Arizona State University are working to flip the process on its head. Instead of making a material and then finding out what it can do, they are starting from the end — deciding what properties a material should have and then designing the material to have those traits. These could range from strength to flexibility to electrical conductivity and more.
A need for structure
“We already have performance in mind. So we need to ask ourselves, what are the things you can change, what can you play with to give you this performance? The thing that we play with is the material microstructure,” said Yang Jiao, an assistant professor in ASU’s Ira A. Fulton Schools of Engineering.
For example, if you look at a piece of metal, it appears to be one uniform material. But most metals are alloys made from two or more elements, such as copper and aluminum.
“You melt them together, stir and cool again. As you cool it, the distribution of the components will be different in different parts of the metal,” Jiao said.
At high temperatures, copper and aluminum mix together evenly, but as they cool the copper forms clusters. The differences are not visible to the naked eye, but they can be seen under a microscope. This structure, with its clusters of copper, affects the properties of the material.
Think about building a house out of bricks. If you just stack bricks on top of each other in side-by-side columns, your house will not be very strong. But if you stagger the bricks, the structure will be much stronger.
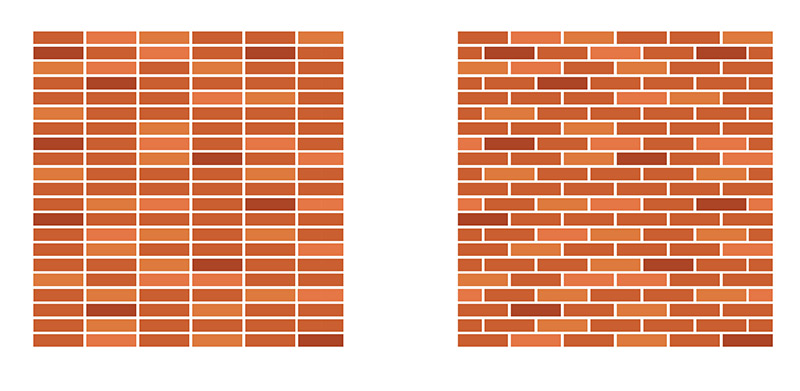
It's easy to see how structure affects strength if you think about a brick wall. Bricks stacked directly over one another, in columns (left), will product a structurally weaker wall than one in which the bricks are staggered.
It’s easy to see how staggered bricks make a stronger wall. It’s much harder to figure out how the structure of a titanium alloy helps it withstand repeated stresses without breaking — also known as fatigue strength. This is the challenge that Jiao is confronting with his colleagues, Yi “Max” Ren and Yongming Liu. All three are faculty members in the Fulton Schools' School for Engineering of Matter, Transport and Energy.
“You have a target property — I want a fracture strength as high as possible. Then what kind of microstructure will achieve that? Instead of evaluating existing materials, I want to find the structure that will match the property,” said Ren, an assistant professor who studies design optimization.
Making a connection
Scientists can figure out the microstructure of a material that already exists. Jiao develops computer simulations that can analyze that microstructure and determine what properties it will have. The simulations are based on data from experimental testing.
What he can’t do, yet, is go in reverse. The computer simulation can say, “This structure will give you this property, and that structure will give you that property.” But it doesn’t explain why. So the researchers don’t know what specific characteristics of a structure cause it to have the properties it does.
This is where Ren’s expertise comes in. He is developing software to help the computer identify which features of a microstructure are important to specific properties. He is drawing on deep learning technologies, a branch of artificial intelligence in which software learns to recognize patterns. This is how Facebook recognizes your friends in a photograph and how Amazon makes personalized recommendations.
“We want the machine to learn by itself what structural features influence a material property,” he said.
The computer will analyze images of different microstructures pixel by pixel. Pulling data from Jiao’s simulations, the software will look for patterns in the images that correlate with specific properties.
“The machine sees several images and tries to make puzzle pieces of these images. You want to come up with a small set of pieces that can be used to reconstruct all of these images. Then you are free to recombine the pieces to get new images,” he said.
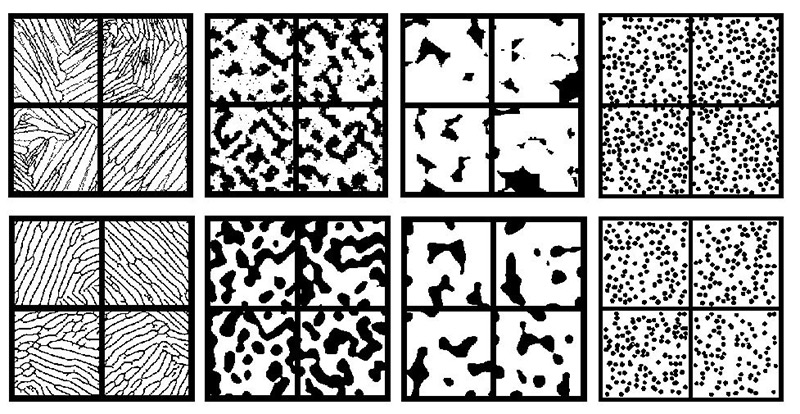
Across the top, images of original samples of titanium alloy, lead-tin alloy, Fontainebleau sandstone and spherical colloids (from left to right). The computer learned from these samples and created the reconstructions shown across the bottom. Image by Ruijin Cang, Yang Jiao and Yongming Liu
The team is also working to reduce the number of pixels the computer needs to analyze. This is similar to compressing a high-resolution photo as a JPG file. Photo compression removes pixels to reduce the file size and the computing power needed to work with it, while still leaving a recognizable image. The ASU researchers want to reduce the computer’s workload in analyzing microstructures. But they don’t want to lose key information about which structures create useful properties.
Ultimately, the process will make materials development less costly and time-consuming, potentially reducing the development cycle from about 10 years to about two.
“Another benefit is that when we do this type of study, we generate a huge database which is shared among the community. Anyone can access these,” Jiao said.
Putting materials to the test
Once the team has identified the best structure, they’ll need to produce a sample of the material and test it out in the lab. In this case, that means pulling and releasing the material over and over to find out how quickly it gets fatigued.
Material fatigue is what caused the fuselage of a Southwest Airlines jet to rupture mid-flight in 2011, ripping a 5-foot gash in the upper cabin. (Fortunately, the pilot was able to make an emergency landing without any fatalities.)
Every time an airplane takes off, the cabin inside is pressurized so that passengers can survive at high altitude. This puts force on the body of the aircraft. With every landing, the cabin is depressurized, removing that force. After thousands of these flight cycles, the metal of the fuselage gives out and begins to develop cracks, which are often microscopic and require special tools to detect.
“Aircraft is safe, much safer than before,” noteed Liu, a mechanical and aerospace engineering professor. “But still fatigue is inevitable and a safety concern. We want it to be even safer. People still don’t really understand the very fundamental aspect of fatigue. The variability is huge. This could fail in one year or 100 years. People don’t really know why. One of the primary reasons comes from the microstructure.”
Liu is an expert in mechanical structures who works with a variety of tools at ASU to test and image materials. For example, ASU has a palm-size fatigue testing machine that can fit into a scanning electron microscope.
“If you don’t know what happens, you go in and see it,” he explained.
One major challenge the team faces is that it may not be possible to reproduce the ideal microstructure using current manufacturing techniques.
“It’s probably not possible at this stage to reproduce the design exactly,” Jiao said. “We can produce something similar and do the testing. We need to come up with a microstructure with a certain tolerance of uncertainty.”
Transformative ideas
Although computational materials design is a fairly new field, it’s a hot topic nationwide, spurred by the federal Materials Genome Initiative. The multi-agency initiative was launched in 2011 to support institutions in discovering, manufacturing and deploying the advanced materials that are essential to economic security and human well-being.
ASU’s work is supported through a National Science Foundation EAGER grant, which funds early-stage work on potentially transformative ideas.
“There is a growing interest in this area because people realize it will change how materials will be developed. It saves a lot of time and money. It will also bring a lot of benefit to fundamental physics and mathematics,” Liu said.
“We are lucky that we have complementary expertise,” he added. “We’re a strong team. I’m a computational person, so I know it’s extremely important for me to work with experimentalists. We have a very nice characterization group, testing group. And the microscopy facility here is world-class.”
Liu notes that ASU provides an excellent environment for collaboration, not just within a school but across disciplines. In fact, he recently won a $10 million grant from NASA to lead a multidisciplinary team in studying how to integrate the complex data sources that are driving the future of air traffic management systems.
“We’re addressing very large problems for complex systems. The problem is not too little data, it’s too much. How do you fuse this data to get what you want? You need to go beyond, working with very different schools, including human factors,” he explained.
He added: “At ASU I don’t need to go outside. I get whatever I need from ASU.”
Learn more about this research at: http://designinformaticslab.github.io/project-esd/2016/05/25/materialdesign.html. This research is funded through the National Science Foundation EAGER award No. 1651147.
More Science and technology

ASU-led space telescope is ready to fly
The Star Planet Activity Research CubeSat, or SPARCS, a small space telescope that will monitor the flares and sunspot activity…

ASU at the heart of the state's revitalized microelectronics industry
A stronger local economy, more reliable technology, and a future where our computers and devices do the impossible: that’s the…

Breakthrough copper alloy achieves unprecedented high-temperature performance
A team of researchers from Arizona State University, the U.S. Army Research Laboratory, Lehigh University and Louisiana State…