ASU engineer looks to improve next-gen materials for solar cells
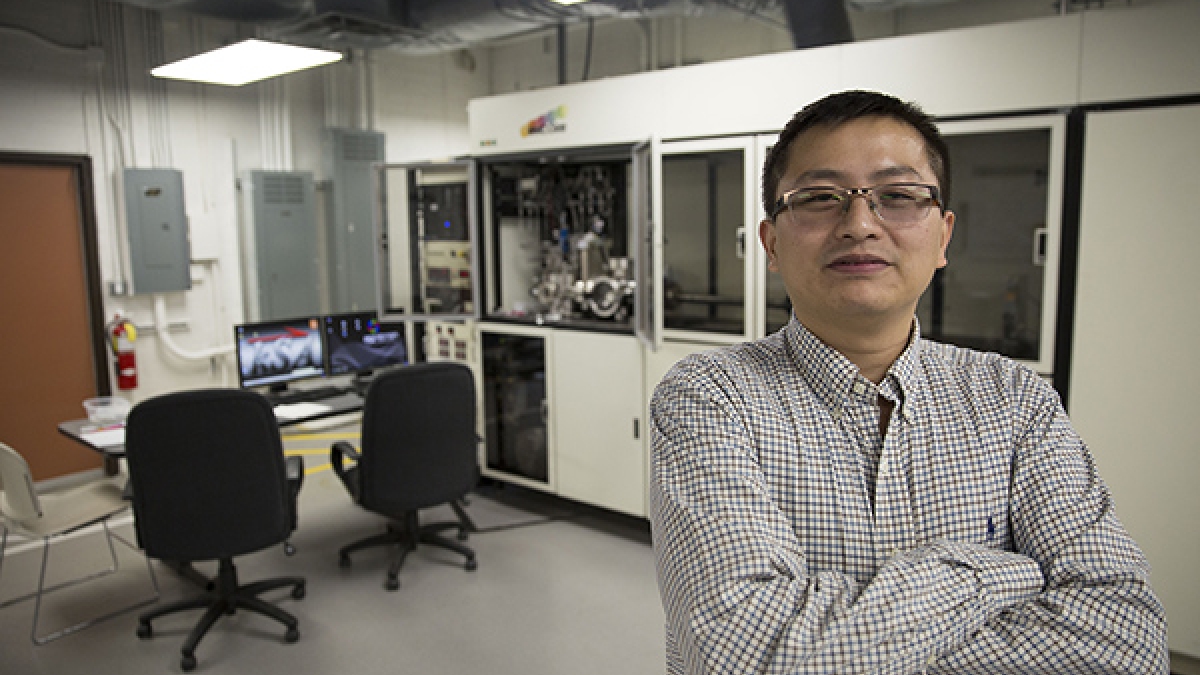
Electrical engineering Assistant Professor Yuji Zhao stands in his Metal-Organic Chemical Vapor Deposition lab on the Tempe campus, where he works with gallium nitride, a compound with unique properties. Zhao's research is focused on exploring gallium nitride's use in optoelectronics and high-power and high-frequency devices. Photo by Pete Zrioka/ASU
New findings by an Arizona State University engineer outline new advances in solar cell technology and point to the incredible potential of the material used to fabricate the cell — gallium nitride.
A research paper published April 17 in Applied Physics Letters details electrical engineering Assistant Professor Yuji Zhao’s efforts to use gallium nitride to create a high-performance solar cell capable of operating under extremely high temperatures.
Gallium nitride is a unique compound, the properties of which make it an excellent candidate for use in optoelectronics and high-power and high-frequency devices.
“This material is remarkable and has such high potential,” Zhao said.
Zhao notes that some have called gallium nitride the next silicon — the ubiquitous material that serves as an integral component of many of our electronics, from computer chips and solar cells to transistors and integrated circuits. Gallium nitride could prove to be superior to silicon, and Zhao’s work is paving the way toward faster, more efficient and higher-powered devices of all kinds.
Zhao first began working with the material under pioneering researcher Shuji Nakamura of the University of California, Santa Barbara. Nakamura was awarded the Nobel Prize in Physics in 2014 for developing efficient blue-light-emitting diodes, which has enabled bright and energy-saving white-light LEDs.
While working toward his doctorate, Zhao focused on employing gallium nitride for use in LEDs and lasers. Now he’s taken the material far beyond optoelectronics, expanding its use for solar panels, power systems and more. His exploration of the material’s myriad uses has earned him support from both NASA and the U.S. Department of Defense.
In 2015, Zhao was awarded a prestigious Early Career Faculty Space Tech Research Grant from NASA, a first for Fulton Schools faculty. The award supported the focus of his Applied Physics paper to create high-temperature resistant solar cells.
“They have high hopes for this project. They seem to believe this is one of the most promising methods to achieve their goals,” Zhao said.
Currently, Zhao is prototyping the solar panels, and will begin thermal testing soon.
“It’s not a question of whether or not the panels will work under high temperatures, but of how efficiently they will perform,” Zhao said.
More recently, he received a $300,000 award from the DOD’s Defense Threat Reduction Agency, which supports basic research to counter weapons of mass destruction. Zhao’s work with the DTRA is focused on using aluminum nitride to create transistors that can withstand high voltage and resist radiation damage.
To test this, he and his team will construct a Schottky Diode — a basic two-terminal electric component — and place it in a radioactive environment, subjecting it to different types of radiation in varying doses and rates of exposure. This radioactive stress test will eventually cause degradation in performance in the diode. That’s when Zhao will turn to materials studies to determine how to improve the material’s resistance and performance.
The applications are far reaching, such as for more robust power electronics and communications systems, but the DTRA is primarily interested in military devices that would remain operational following a radiation event, Zhao said.
Zhao credits his success in attracting funding to refine materials and explore their uses to the work being done in his cutting-edge Metal-Organic Chemical Vapor Deposition lab on the Tempe campus.
“One of the key reasons I was awarded these grants was first my background with this work, but also the capability of the MOCVD lab,” Zhao said. “The equipment we use is industry standard, not different from what you’d find in a major company.”
The lab required an estimated investment of $800,000 to set up and became fully operational in fall 2016.
He envisions the lab as a truly interdisciplinary space, and not only because his research draws on the expertise of physicists, materials scientists and device designers. Zhao wants the MOCVD lab to be an unparalleled resource for all of the Fulton Schools.
His ultimate goal mirrors the Nobel Prize description: developing science and tech for the betterment of humanity. He’s chosen refining and improving next-generation materials, such as gallium nitride, as his avenue to do so.
“The idea is to benefit as much of ASU as possible, which will hopefully extend outside of the university as well,” Zhao said.
More Science and technology
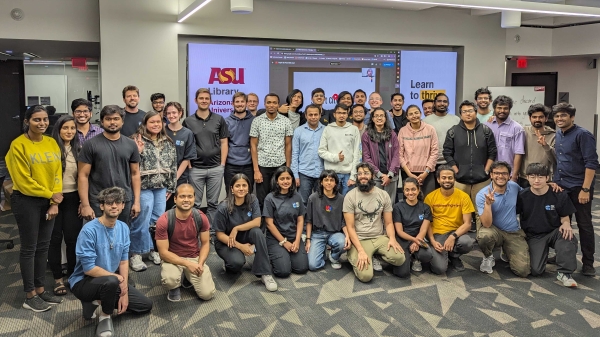
SpaceHACK highlights student solutions to environmental challenges, digital divide
By Adrianna Nine About 250 students from around the world convened online and at Arizona State University on March 22 for the…

New AI for a new era of discovery
As the legend goes, in 1665, Sir Isaac Newton sat in his garden at Woolsthorpe Manor in England and looked on as a lone apple…
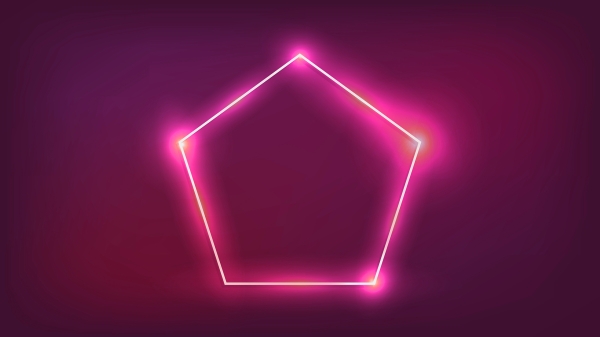
ASU receives 3 awards for research critical to national security
Three researchers in the Ira A. Fulton Schools of Engineering at Arizona State University have received grant awards under the …